In recent years, polyurethane products have become increasingly popular, such as the cold storage panels produced by Harbin Dong'an Building Sheets in China, which are made of polyurethane materials.
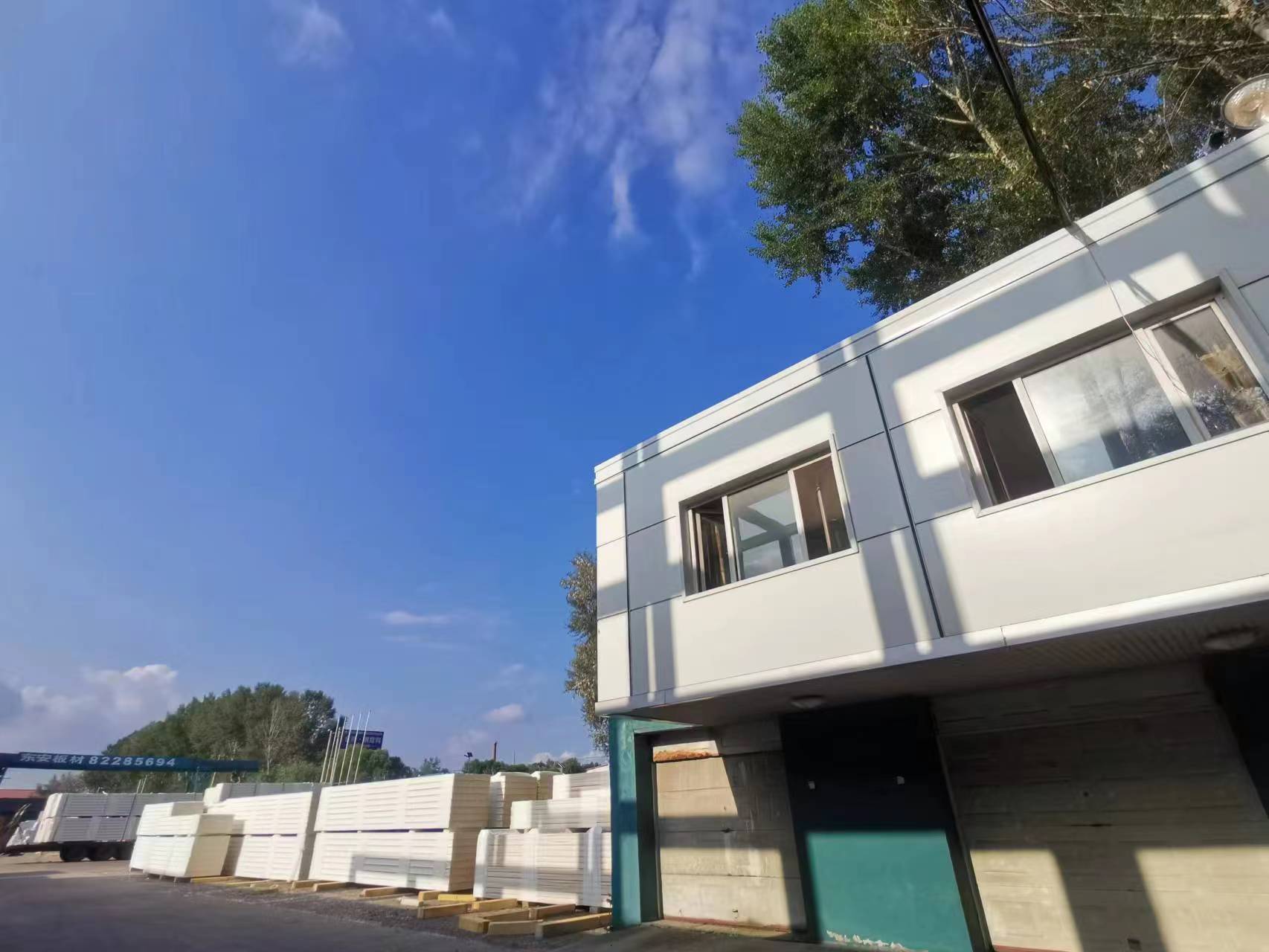
Generally, polyurethane can be divided into thermosetting and thermoplastic, and can be made into polyurethane plastics (mainly foam plastics), polyurethane fibers (spandex), and polyurethane elastomers. Most polyurethane materials are termed thermosetting, such as soft, hard and semi-rigid polyurethane foams.
The recycling of polyurethane often adopts physical recycling methods, as this method is relatively effective and economical. Specifically, it can be divided into three recycling methods:
This method is the most widely used recycling technology. The soft polyurethane foam is crushed into several centimeter pieces by a grinder, and the reactive polyurethane adhesive is sprayed in the mixer. The adhesive used is generally polyurethane foam combination or NCO terminated prepolymer based on polyphenyl polymethylene polyisocyanate (PAPI). When using PAPI based adhesives for bonding and molding, steam mixing can also be introduced. In the process of bonding waste polyurethane, add 90% waste polyurethane and 10% adhesive, mix evenly, or add some dyes, and then pressurize the mixture.
The bonding forming technology not only has great flexibility, but also has great variability in the mechanical properties of the final product. The most successful recycling method of polyurethane products is to produce recycled polyurethane foam by bonding waste foam such as soft foam leftovers, which is mainly used as carpet backing, sports mat, sound insulation materials and other products. Soft foam particles and adhesives can be molded into products such as car bottom pads at a certain temperature and pressure; By using higher pressure and temperature, hard components such as pump housings can be molded out.
Rigid polyurethane foam and reaction injection molding (RIM) polyurethane elastomer can also be recycled by the same method. Mixing waste particles with isocyanate prepolymers for hot pressing forming, such as manufacturing pipe brackets for pipeline heating systems. |
2、Hot pressing molding
Thermosetting polyurethane soft foam and RIM polyurethane products have certain thermal softening and plasticity properties in the temperature range of 100-200 ℃. Under high temperature and pressure, waste polyurethane can be bonded to each other without the use of adhesives. In order to make the recycled products more uniform, it is often necessary to crush the waste and then heat and press it into shape.
The forming conditions depend on the type of waste polyurethane and the recycled product. For example, polyurethane soft foam waste can be hot pressed for several minutes at a pressure of 1-30MPa and a temperature range of 100-220 ° C to produce shock absorbers, mudguards, and other components.
This method has been successfully applied to the recycling of RIM type polyurethane automotive components. For example, car door panels and instrument panels can be manufactured with approximately 6% RIM polyurethane powder and 15% fiberglass. |
3、Used as filler
The polyurethane soft foam can be turned into fine particles by low-temperature crushing or grinding process, and the dispersion of such particles is added to polyols for manufacturing polyurethane foam or other products, which not only recovers the waste polyurethane materials, but also effectively reduces the product cost. The content of broken powder in MDI based cold cured flexible polyurethane foam is limited to 15%, and 25% of broken powder can be added in TDI based hot cured foam at most.
One process is to add pre chopped waste foam waste into soft foam polyether polyol, and then wet grind it in a suitable mill to form a "recycled polyol" mixture containing fine particles for manufacturing soft foam.
Waste RIM polyurethane can be crushed into powder, mixed with raw materials, and then manufactured into RIM elastomers. After the waste polyurethane rigid foam and polyisocyanurate (PIR) foam waste is crushed, it can also be used to add 5% recycled material in the combination to produce rigid foam. |
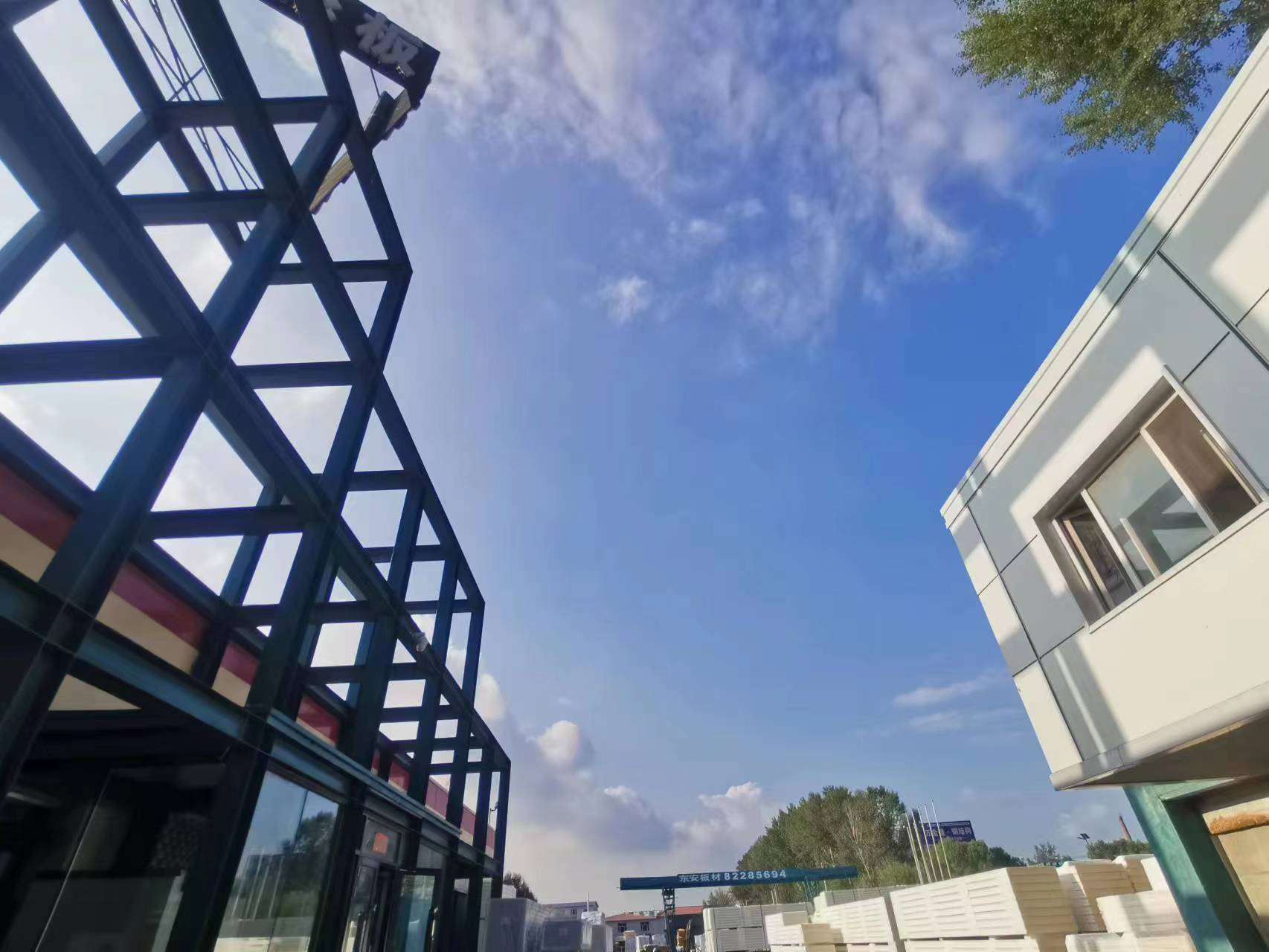
In recent years, a new chemical recovery method has emerged
The University of Illinois team led by Professor Steven Zimmerman has developed a method for decomposing polyurethane waste and converting it into other useful products.
Graduate student Ephraim Morado hopes to reuse polymers through chemical methods to solve the problem of polyurethane waste. However, polyurethane has extremely high stability and is made from two components that are difficult to decompose: isocyanates and polyols.
Polyols are the key to the problem, as they are extracted from petroleum and are not easily degraded. To avoid this difficulty, the research team adopted a more easily degradable and water-soluble chemical unit acetal. The degradation products formed by dissolving polymers with trichloroacetic acid and dichloromethane at room temperature can be used for the production of new materials. As proof of concept, Morado can convert elastomers widely used in packaging and automotive parts into adhesives.
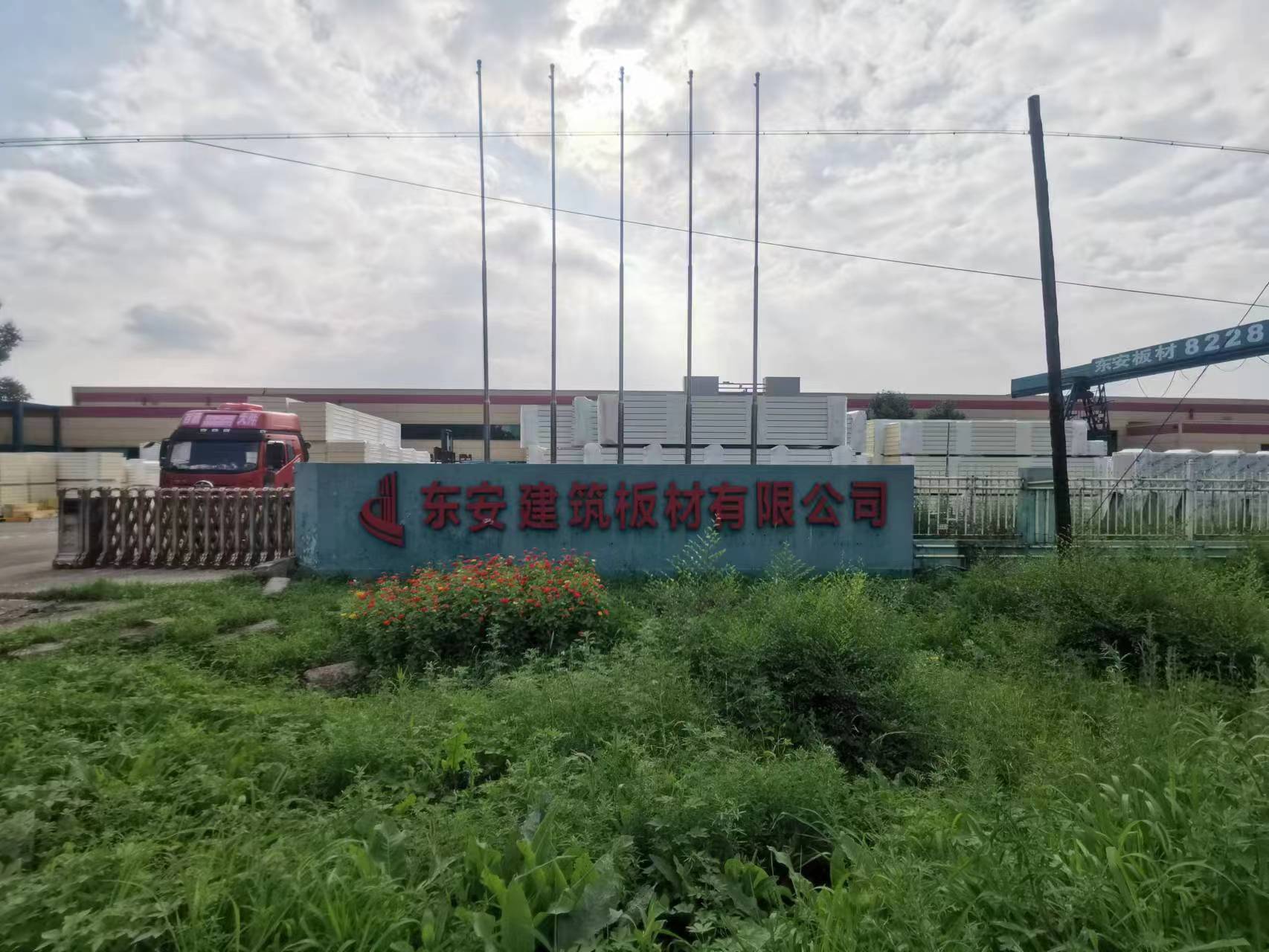
However, the biggest drawback of this new recycling method is the cost and toxicity of the raw materials used for the reaction. Therefore, researchers are currently trying to find a better and cheaper method to achieve the same process by using mild solvents such as vinegar for degradation.
In the future, Harbin Dong'an building sheets company will also closely follow the industry's innovation and continue to invest in technology and environmental protection technology, continuously innovating to make Dong'an's polyurethane panels more environmentally friendly and healthy. We also believe that there will be more new environmental protection technologies born in the future.
Post time: Nov-09-2023